Predict When Your Parts Fail
Predictive Maintenance of Key Components Finally at Your Fingertips
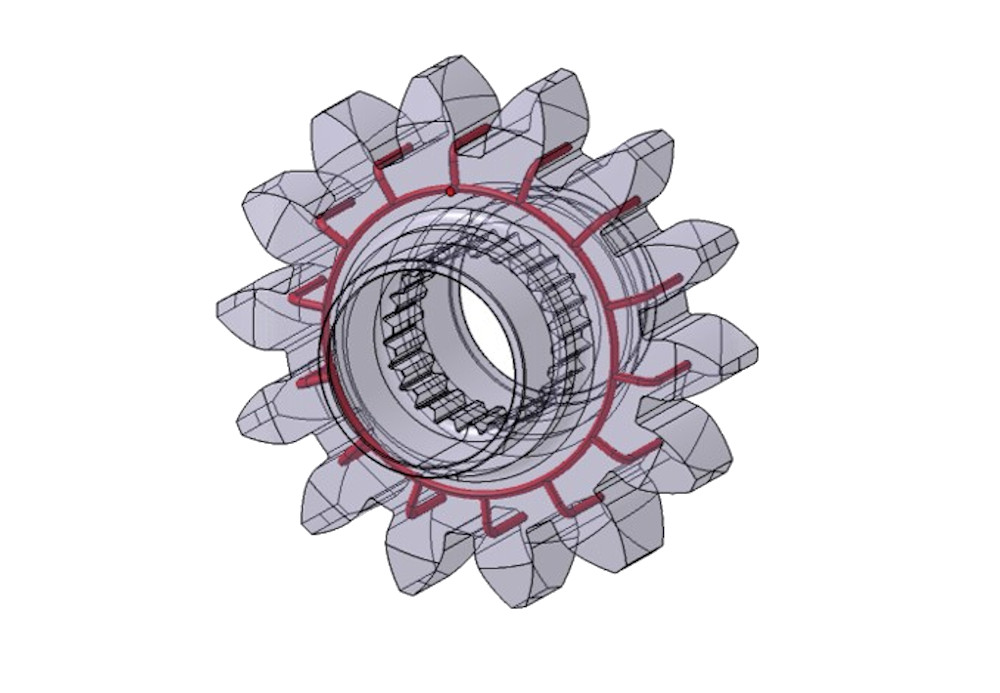
Our Predictive Maintenance Solution
We give you access to robust predictive maintenance of safety critical or strategic maintenance components via our patented effective Structural Health Monitoring (eSHM) technology.
The eSHM Process
The eSHM product optimization process is as follows:
- Carefully selected, key maintenance components are redesigned and equipped with strategically positioned, internal channels.
- After component redesign, the parts are realized by the means of (Polymer or Metal) 3D Printing, post-processed and thoroughly tested on quality and performance.
- When the parts are finished, the integrated channels are either pressurized or vacuumed and the corresponding pressure or vacuum levels are closely monitored by off-the-shelf pressure sensors.
- During usage, loads will translate into pressure fluctuations that can be accurately monitored. When fatigue cracks initiate, the pressure level will gradually drop, which can trigger an alarm and enable predictive maintenance.
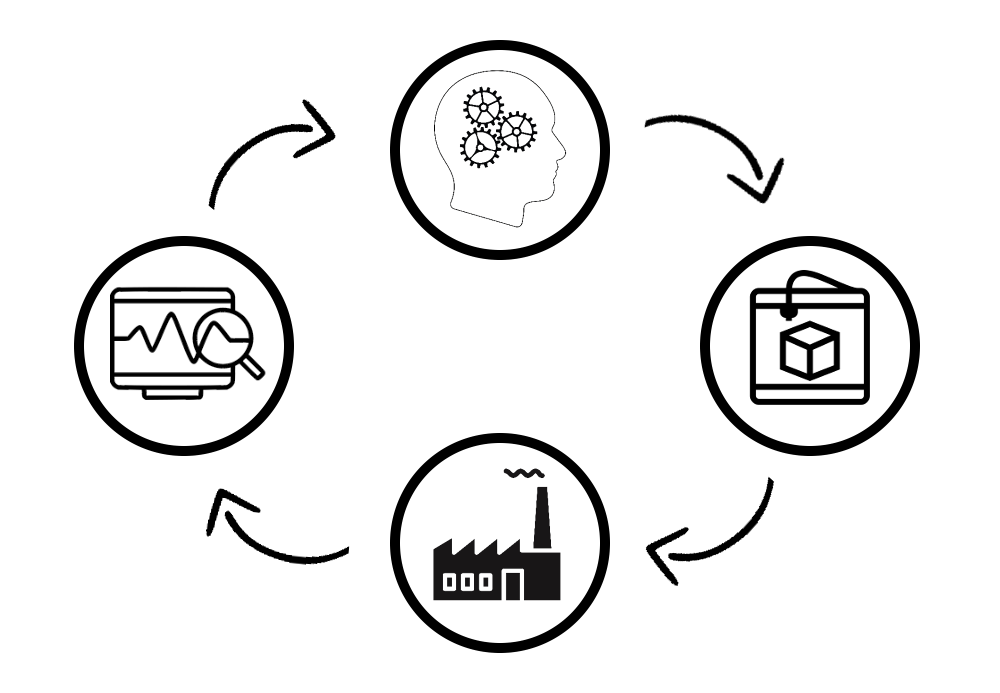
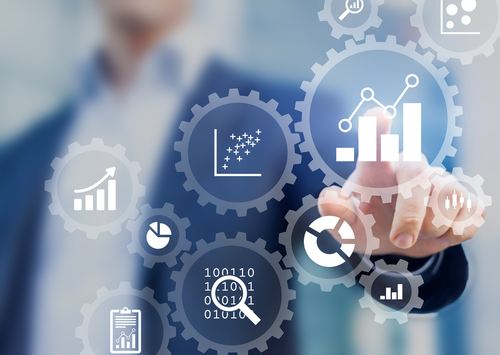
Key Benefits
- Robust: The eSHM system is embedded: If the eSHM system “breaks”, this would mean that the part is broken.
- Accessible: Pressure Sensor In- and Outlets can be positioned at accessible locations.
- Qualification: The eSHM system is flexible and a wide range of industry standard pressure sensors in all size ranges can be used.
- Interpretable Data: Pressure data can be easily interpreted.
- Flexibility of Maintenance Strategies: Parts can be monitored during or after the process, a large or small amount of data can be collected, the system can work on- or offline,…
Academically Proven
The eSHM has been presented at numerous prestigious academic conferences around the world and received numerous positive opinions from peers in the field of structural health monitoring.
The system concept was optimized in order to make sure that the system has no impact on the fatigue strength performance of the components but maximizing the structural integrity detection and monitoring capabilities.
The robustness of the system has been mechanically tested and validated. It has proven to be able to obtain a damage detection capability of 100% by stopping the test machine before critical failure occurred and this for more than 100 test samples. Currently the system has reached a technological readiness level of 5, which was validated by industrial experts.
Meet the Inventors
Dieter De Baere (right) is an engineer-researcher with a passion for aeronautics and for optimizing sustainable mechanical products. He has the ambition to stimulate the adaptation of components with integrated sensing functionality created by additive manufacturing, in order to promote sustainable products in a safe manner.
Michaël Hinderdael (left) is a science-enthusiast and post-doctoral researcher at Vrije Universiteit Brussel, with a research focus on embedded structural health monitoring solutions for additively manufactured components. He holds an MSc and PhD degree in Engineering from the Vrije Universiteit Brussel.
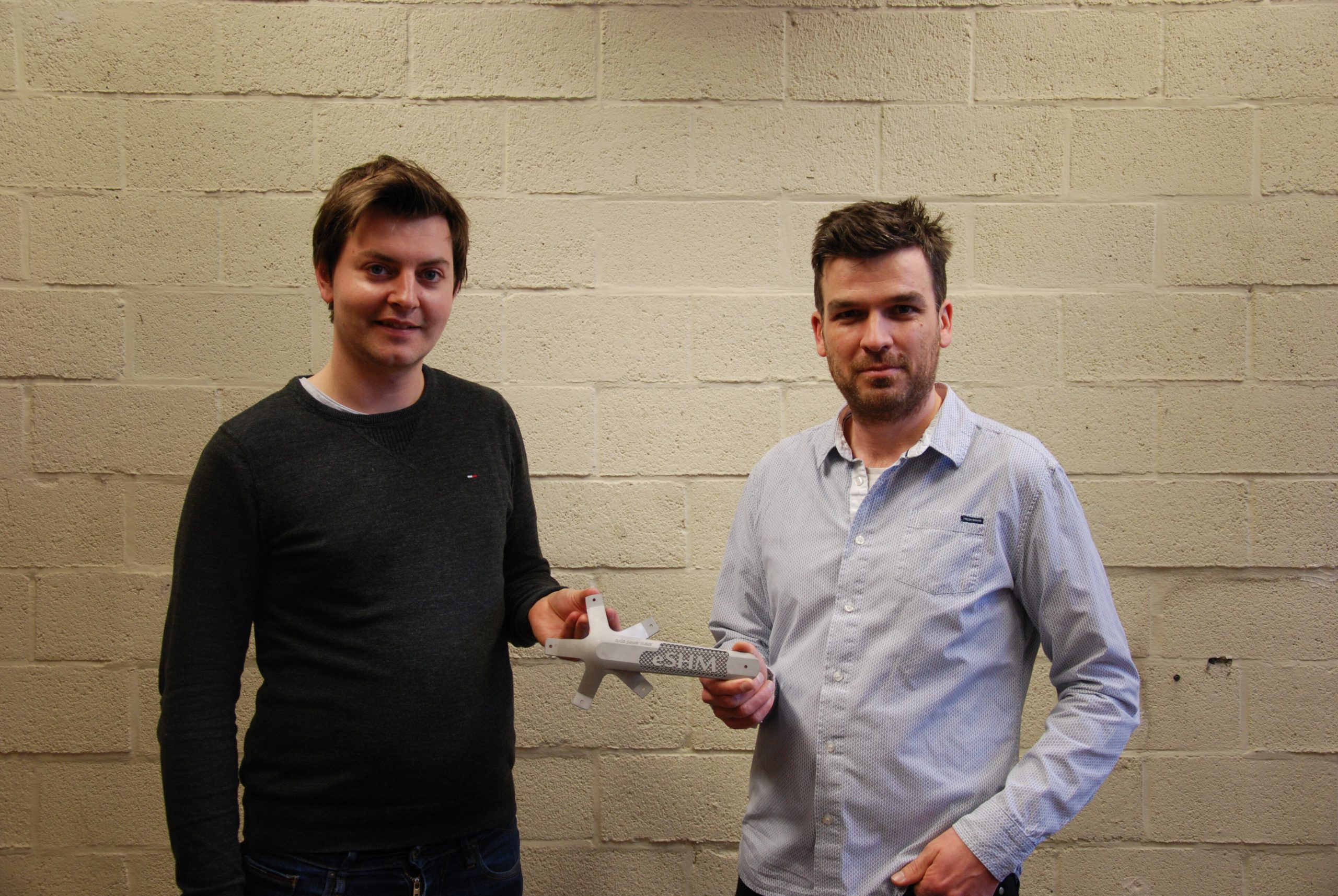
Get In Touch
If you'd like to discover more on the eSHM system, feel free to reach out to us.